247Uptime: Optimal maintenance of your machines
Careful maintenance of your production machines saves money, but requires know-how and regular servicing. You have competent specialists and external service providers for this.
247Uptime is the perfect support for all employees who are entrusted with maintenance tasks. As a simple maintenance tool, 247Uptime organizes the collaboration of your specialists – especially for autonomous maintenance and the involvement of external service providers.
At the same time, simple documentation of all incidents, solutions and maintenance work ensures that knowledge is built up over the long term. In this way, you secure the know-how about your machinery and make it accessible to all employees.
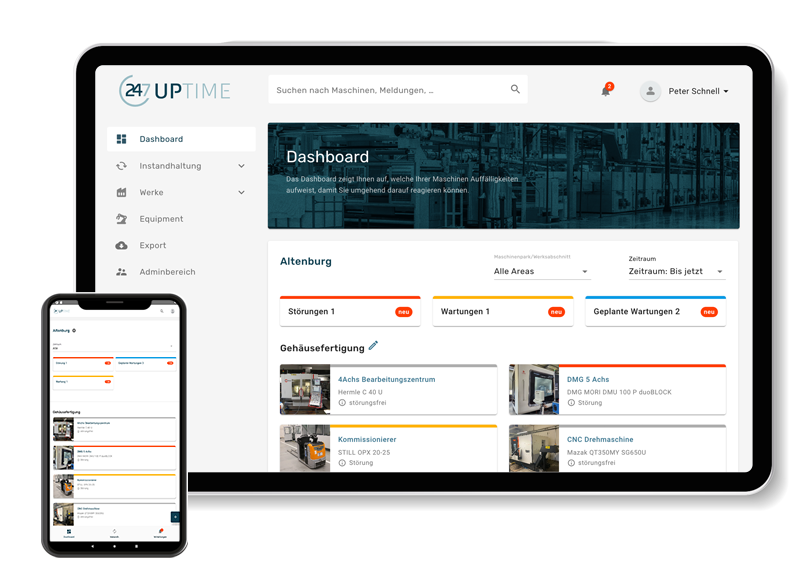
Dashboard: So you always know what’s going on
or where there’s something to do.
247Uptime: Maintenance management pays off immediately
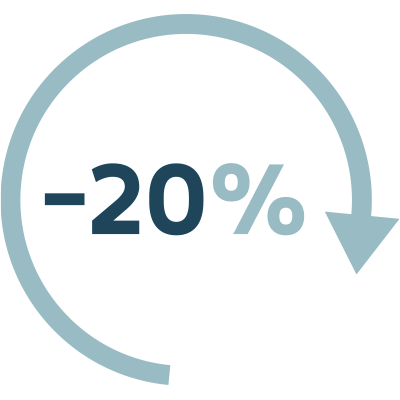
Reduction of
maintenance costs
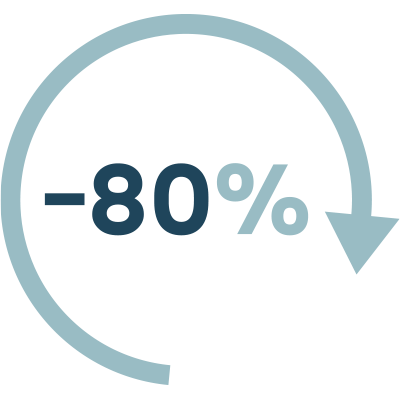
Reduction of
unplanned downtime
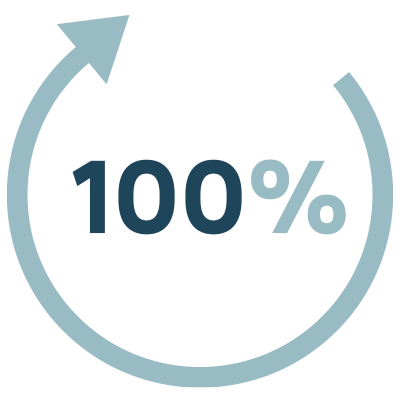
Increased transparency
and safeguarding know-how
Maintenance scheduling for your machinery
Carrying out maintenance and inspections is an essential part of preventive maintenance. With the help of maintenance planning from 247Uptime, you always have an overview of all measures. Whether in accordance with manufacturer specifications or your maintenance strategy, you can use our maintenance software to optimize your maintenance processes.
- Machine-specific planning of maintenance and inspections
- Plant overview in the maintenance calendar with reminders via email and push notifications
- Classification of maintenance and inspections
- Detailed description of the maintenance procedure
- Documentation of the maintenance carried out and storage in the machine history
- Recording of planned and actual costs and times for each maintenance task carried out
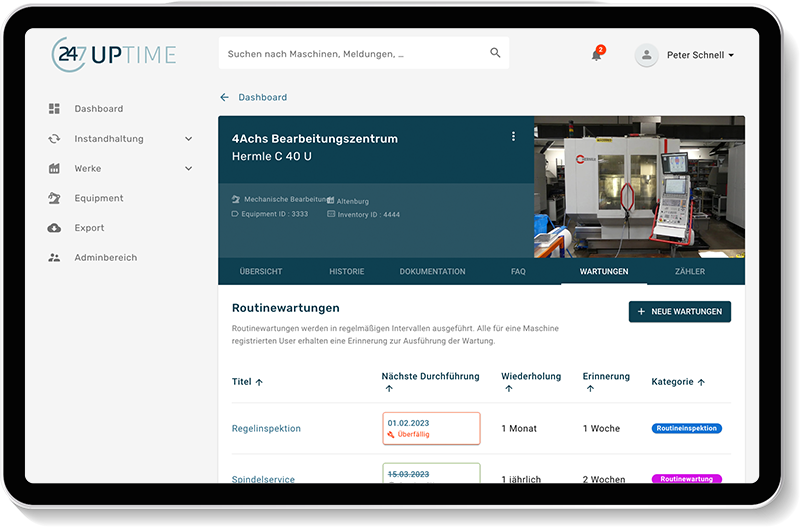
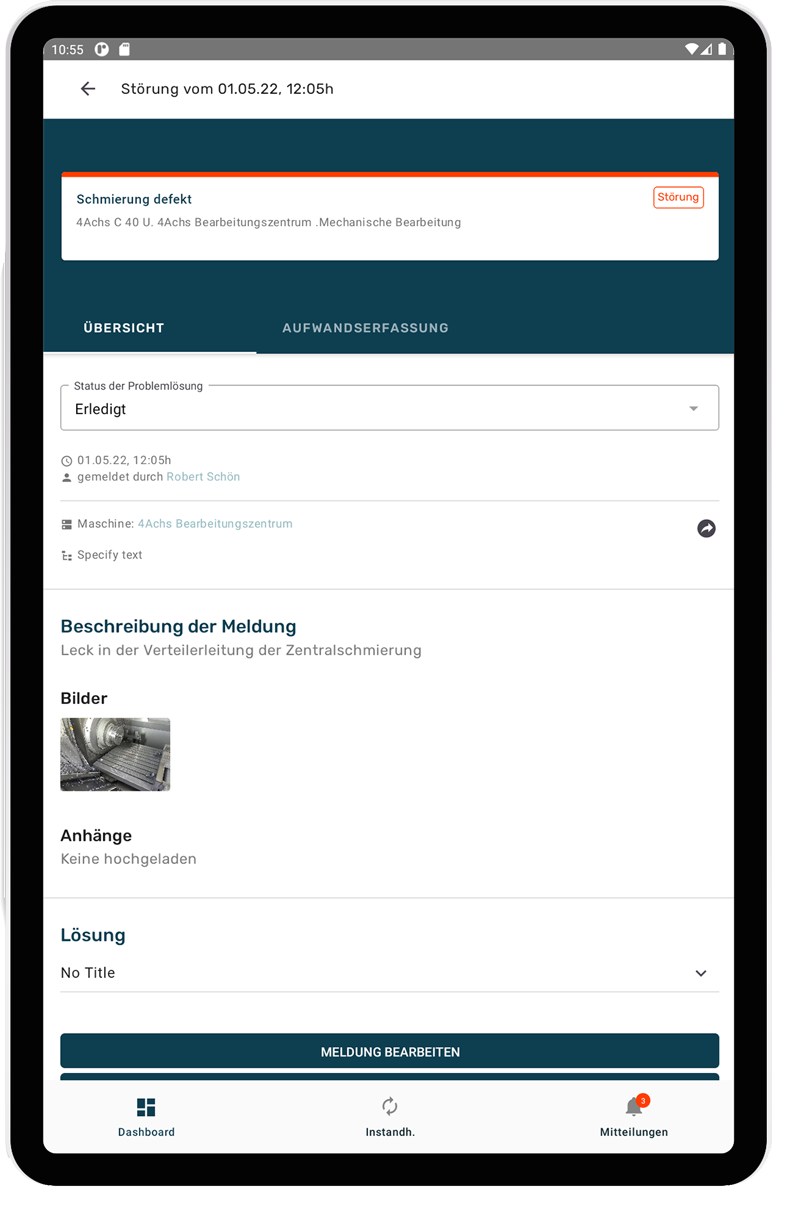
Error management: mobile and always up-to-date
247Uptime is designed as a mobile maintenance solution, making it particularly easy to document machine life. Whether an unplanned downtime or just an anomaly: any incident can be recorded, documented and reported with the help of messages. If there is a major problem, the solution can also be documented and stored in the digital machine log.
- Documentation of incidents with text, photos, videos and documents
- Status of the report: open, in progress, completed.
- Processing of reports for additions or corrections
- Sending the fault report to the manufacturer’s service department
- Classification of the report: fault, abnormality, message, etc.
- Storage of the message in the machine history
- Documentation of problem solutions
- Recording of costs and times
Digital knowledge management secures your machine know-how and makes it available at all times
As a platform for knowledge management, 247Uptime focuses on the central provision of all documents in the mobile machine file on the one hand and on building up experience in dealing with your machinery on the other. This is particularly valuable for our customers, as many experienced machine operators and maintenance staff will soon be retiring.
- Provision of all media relating to the machine in the machine management system (documents, videos, plans, etc.)
- Provision of internal documents to standardize the procedure (e.g. across locations)
- Clear FAQs on the machines
- Digital machine log with all incidents and problem solutions
- Search function to quickly find solutions in documents or previous incidents
Simple organization of maintenance tasks in small companies
Professional maintenance of production facilities saves money, increases availability and contributes to a stable high quality of the parts produced. The effectiveness of maintenance can be measured in various key figures such as MTTR, MTBF or OEE and is part of numerous production management approaches such as TPM. For this reason, large companies train entire departments with the task of professional maintenance management. In small companies, on the other hand, maintenance is often only carried out by a few employees and often only in addition to numerous other tasks. With 247Uptime, this is not a disadvantage per se. After all, whether the maintenance task is also implemented effectively in small production facilities is primarily a question of organization and transparency. 247Uptime offers an optimal platform for this as a simple and intuitive maintenance management software.
- No more missed routine maintenance thanks to numerous reminder functions
- Optimal organization of collaboration across locations
- Optimal standardization of maintenance across locations
- Optimal integration of external service providers and manufacturer service
- Transparency about current incidents and planned actions on the plant dashboard
- Cost and effort recording to analyze and improve the maintenance strategy
- No Excel where it doesn’t belong
Core features
Dashboard for a quick overview
Machine file with documents, FAQs and other information
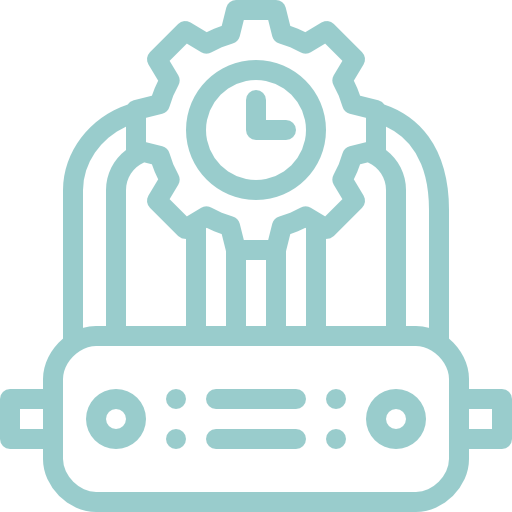
Machine history and digital machine logbook
Recording of meter readings
Maintenance planning and maintenance calendar
Documentation of maintenance work
Recording of costs and times
Recording of faults and documentation of solutions
Search function
Mapping of plant structures and equipment pools
Export of all data to Excel
Standard and advanced users
Full offline capability of the app
Attractive and intuitive operation
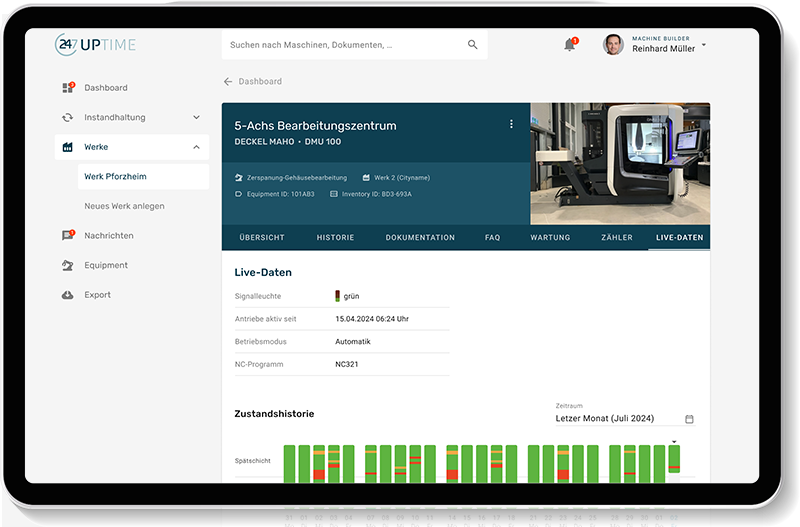
Machine connectivity for maintenance
IoT connectivity enables live monitoring of your machines and production systems or digital predictive maintenance solutions. Such data-driven IoT solutions promise a detailed and always up-to-date insight into the machine status, but initially require a great deal of effort to network the machinery. In small companies, this effort is usually not commensurate with the achievable benefits for maintenance.
247Uptime therefore relies on an approach that does not require an IoT connection to the machines at all, but still promises a high level of benefit and up-to-date transparency.
However, since 247FactoryNet has developed IoT solutions for industry in numerous customer projects, we are also able to establish a network between your machines and 247Uptime at a later date. Read more about our industrial networking solutions here.
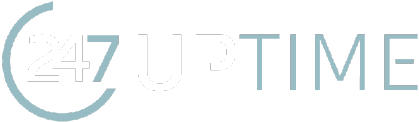
Perfect for mobile and office use!
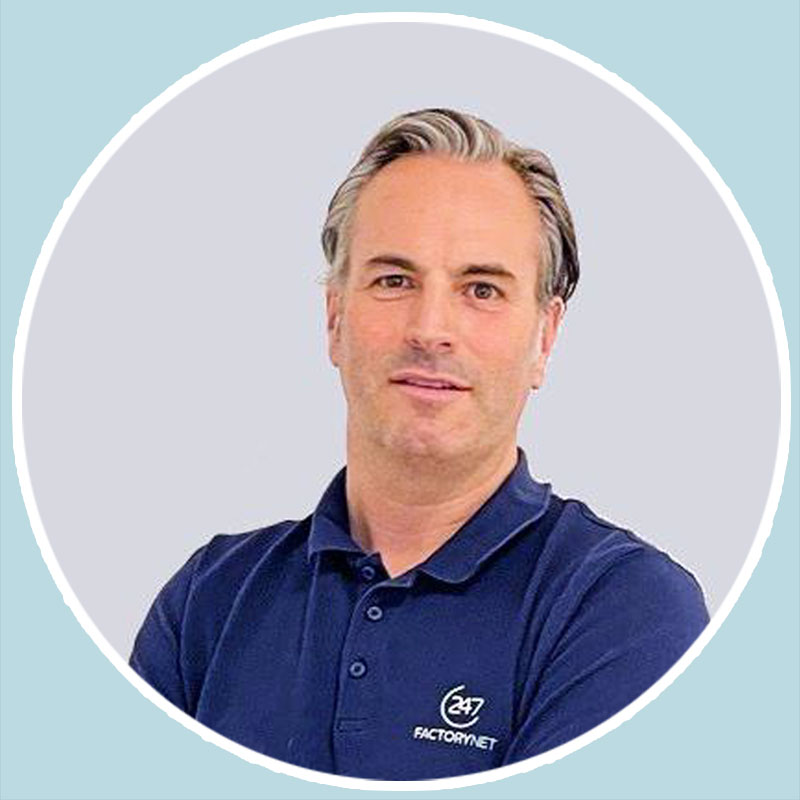
“Small and medium-sized manufacturing companies are the backbone of Germany’s industrial base. We have set ourselves the goal of strengthening these companies with simple digitalization solutions. Therefore, we are constantly improving our solutions. You can rely on us.”
Dr.-Ing Mathias Döbele, Geschäftsführer 247FactoryNet GmbH
Try it out:
Request a 30-day trial now!
247Uptime is the optimal maintenance tool for small and medium-sized industrial production facilities. Test it now for 30 days free of charge!
- Full functionality and maximum performance
- Transfer all your data from the test account
- Hosting in Germany
- Cloud-based, no download required
Quick help with questions and uncertainties.