Mobile apps for machine and plant manufacturers
Mobile apps have long since become part of our daily lives and quite naturally do things that we would not have thought possible just a few years ago.
It is therefore clear that mobile apps are also capable of realizing functions in industry that enable completely new service offerings and business.
Industrial mobile apps will therefore be a matter of course in just a few years – and not just for the younger generation.
Mobile apps have long since become part of our daily lives and quite naturally do things that we would not have thought possible just a few years ago. It is therefore clear that mobile apps are also capable of realizing functions in industry that enable completely new service offerings and business.
Industrial mobile apps will therefore be a matter of course in just a few years – and not just for the younger generation.
New services through mobile apps
The opportunity for machine and plant manufacturers to stand out from the competition with an even better machine is becoming increasingly rare. And this is despite the fact that many customers are more dependent than ever on the support and expertise of their machine suppliers due to increasing complexity and a shortage of skilled workers. Against this background, data-driven services and thus also mobile apps are playing an increasingly important role in supporting machine operators.
The trend towards servicing in machine and plant engineering will be strongly reflected in mobile services or IoT applications. Many machine builders have already launched their first applications. However, relevant new technologies and trends such as augmented reality, 5G, gamification or even artificial intelligence are only just beginning. It is therefore to be expected that the mobile applications that are already in the field today mark only the beginning of a complete revolution of the customer interface.
Read more about our offer for customer portals here
Development of digital services according to the 3-phase model
The development of digital applications differs fundamentally from the known development methods in mechanical engineering. From our diverse project experience, we have developed a 3-phase model that combines the proven methods of software development and startup culture with the requirements of industry. This not only helps our customers avoid the usual painful initial mistakes, but also creates an agile, digital mindset in the company.
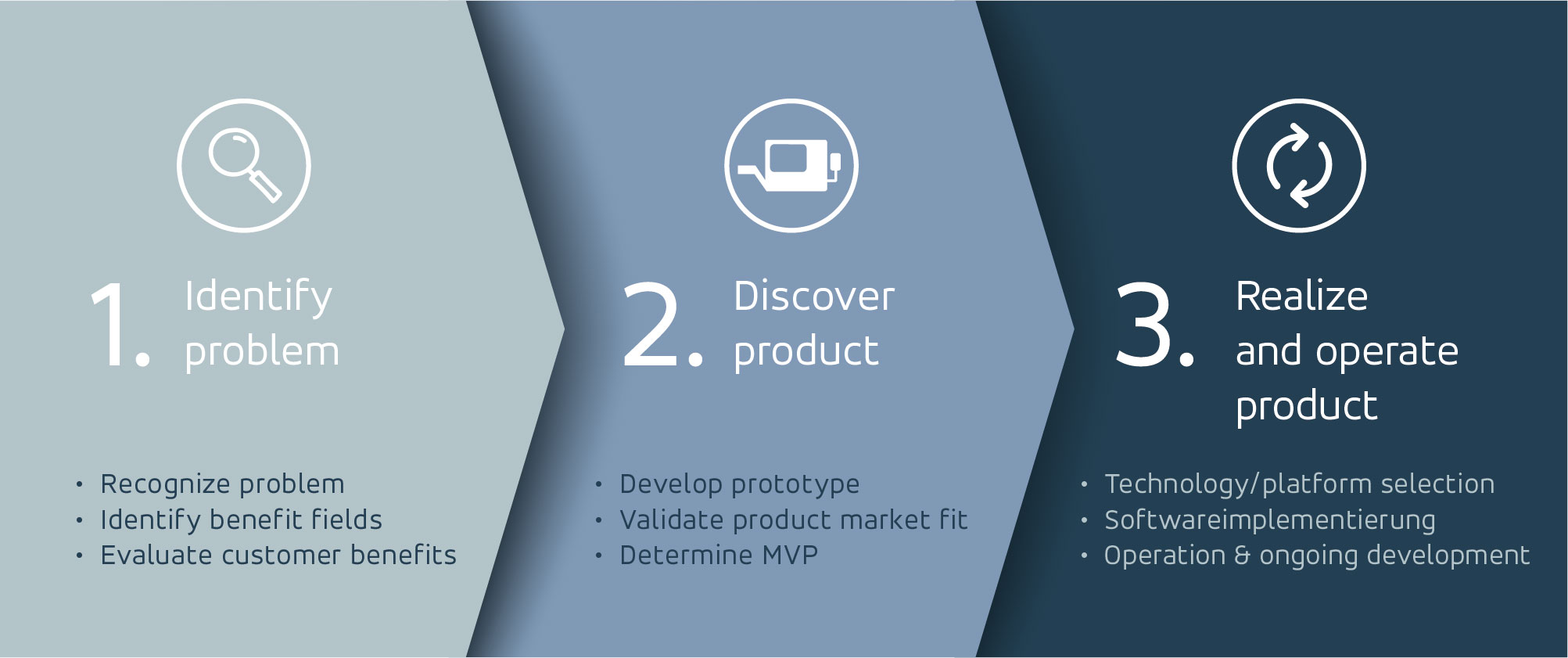
Mobile apps have exciting innovation potential for machine and plant manufacturers
New business models with mobile service apps
Lifecycle services offer numerous potentials for new business models for machinery and plant manufacturers. In future business models, the machine itself will often only play the role of a data supplier, on which smart service business models will be built. In line with the view that “the customer doesn’t want a machine, he wants a produced part,” future business potential will arise much more from the question of how the machines can be digitally integrated into the customer’s processes, how quality monitoring can be automated, or how the machine can contribute to optimizing overall process efficiency. For example, service apps for machine maintenance can create tangible benefits, where the machine builder’s know-how is made available to its customer for its own use.
- Smart services: Make your know-how digitally available to your customer. This will make him better than with your competition.
- Data-Driven Business Models: IoT Applications can be used by your customer 24/7 without incurring additional costs.
- Mechanical engineering apps: From the gearbox to NC control to the cloud. This is the innovation lever of the future.
For innovative machine and plant builders, service has long ceased to refer to the department that supplies spare parts and repairs machines. Service orientation is a trend that affects the entire company and, above all, the business models. Machine as a Service will find its way into future business models through IoT solutions and mobile applications. As a machine and plant manufacturer, you should therefore build up experience with these technologies now.
247FactoryNet supports you on the whole way of developing modern mobile apps
Enhanced user experience: machine, operating panel and web applications
Digitization in mechanical engineering will also be reflected in a completely new user experience that will enable machine operators and maintenance staff in particular to work with the machine in a completely new way. Not only will machines become largely autonomous and, for example, know themselves how to restart them in the event of a malfunction; the users of the machine will also receive role-based user guidance via any interfaces. In this world, mobile apps represent a central technology for offering the customer the highest possible benefit.
Learn more about future-oriented HMI development by 247FactoryNet
Shorter innovation cycles and differentiation through machine building apps
However, digital technologies will also lead to internal changes for machine and plant manufacturers. On the one hand, the potential for differentiation through pure machines will decrease; on the other hand, the potential for differentiation through software will increase significantly. At the same time, this will also significantly increase the innovation cycles within which machine and plant manufacturers will provide new software updates with new and better functions.
This requires new development methods and an agile organization. Learn more about our consulting services in the area of agile methods. Especially in the area of mobile service apps, updates can be brought into the field comparatively easily, since there is no direct connection to the machine. This ensures that the customer can always be offered innovations and new benefits throughout the entire machine lifecycle. This offers new sources of revenue, as new business models of automotive manufacturers also show.
Examples of mobile apps for machine and plant manufacturers
Mechanical engineering apps: this is the innovation lever of the future.
Mobile app development
Mobile apps can be pronounced as native applications that are installed on the mobile device and are thus functional even when the device is not connected to the Internet. Web apps, on the other hand, can provide approximately the same functionality, but run predominantly in the cloud and are only displayed on the device. Web apps are therefore not available offline, but offer the advantage that no local installation is required. However, for more complex applications or for mobile apps with IoT connection to the machines, parts of the software also run in the cloud, which is why only limited functionality is available offline in this case. Which architecture is best for your application depends on the use case that is to be realized and on planned further developments that are already foreseeable.
247FactoryNet supports you on the entire way of developing innovative mobile apps – no matter if it is about the development of first ideas and business models or about software technical implementation of prototypes as well as the final application.
Take advantage of our many years of experience. Because often initial solutions can be created with manageable effort.