Own claim
Based on the objectives and structure of ISO 9000, we have created an individual quality management system that takes into account our special and consistently complex challenges. We have recognized that it is crucial for the sustainable success of our projects to consider the three domains process, information model and software in an integrated way and to solve them in an integrated way. Consequently, the achievement of our quality goals is based on the integration of the three factually separate domains.
The task of our quality management system is to install quality-oriented actions consciously, firmly and measurably in the processes. In this way, we live up to our claim of developing and operating the best products for our customers.
Quality policy
Our own claim to the highest quality is derived from our corporate strategy and the requirements of the market we serve. The quality policy is published in prominent places so that it is always present for all employees.
- We are always approachable for our customers and provide them with a transparent overview of the status of the project.
- We put ourselves in our customers’ shoes, understand their problems, wishes and requirements and transfer these into a digital solution.
- Since customers often don’t understand the details of our solution, we make sure that the solution fits the corresponding problem perfectly.
- If we are not the right partner for a task, we communicate this openly.
- To ensure efficient and targeted software development, we first develop the appropriate test cases and then start the corresponding implementation.
- For the operation of software services for our customers, we apply the highest possible standards in terms of performance and information security.
Executives
The task of the management and executives is to introduce, execute and optimize the quality management system. For this purpose, the necessary resources are provided and the necessary measures are executed. In particular, it is the task of the executives to exemplify quality management. As part of our agile way of working, quality management is also implemented by each employee on his or her own responsibility. The role of the managers is on the one hand coaching to ensure that employees implement things correctly and on the other hand trusting in the conscientiousness of the employees. In addition, recognized quality problems are analyzed and optimized within the framework of the CIP.
Employees
Our culture is based on a high level of personal responsibility of all employees. This principle from the agile way of working provides us with high flexibility and a lean overhead. Accordingly, this naturally also applies to the implementation of our high quality standards. Knowing the quality targets, each employee is not only responsible for the compliance with them in his direct performance area, but also for the dependencies to adjacent areas. This requires each employee to have a fundamental understanding of the overall technical system, which we ensure through regular system reviews in the course of sprint planning. In order to fulfill their tasks in the best possible way, the qualifications of our employees are continuously developed.
Customer
At the beginning of each project, we ensure that the customer’s wishes and requirements have been precisely understood and recorded. In terms of content, the three domains of process, information model and software are already illuminated here and brought into the necessary context. The requirements must be holistically documented in a requirements specification, which serves as the basis for the system design. Frequently, requirements specifications provided by the customer are not complete from our comprehensive point of view. Then – as in the case of a non-existent requirements specification – customer workshops are held to develop the holistic picture.
System-oriented approach
The performance of our products is an interaction of the software we develop, the information that is processed and the processes that are mapped. Only when these three domains interact optimally can a solution be truly powerful and thus achieve satisfactory quality. Our quality management system must therefore create an integrated view in order to detect interactions at an early stage that could later lead to a suboptimal state. The challenge here is that often only the software and its creation process are completely under our control. The process to be mapped is usually specified by the customer or by higher-level processes, and in the case of the information to be processed, there is a highly complex variety of historically grown data models, new lifcycle data and digital information generated by means of AI.
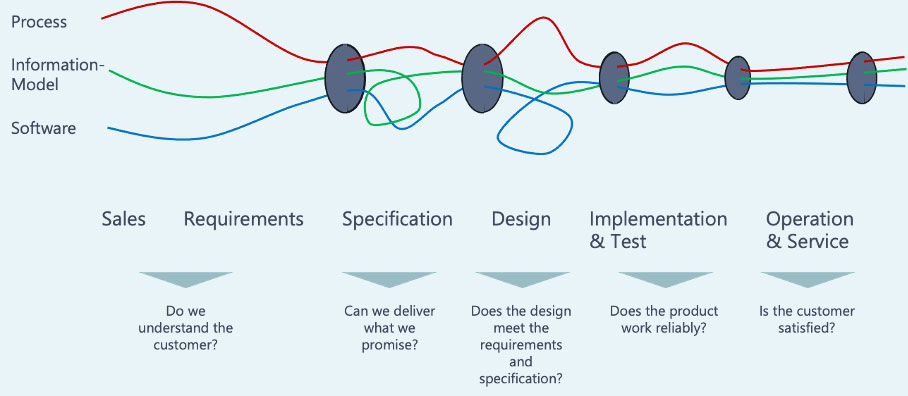
Fig. Systems Quality Approach
Our systematic quality gate approach covers the entire value creation process and requires an integrated analysis of the entire system to reach a milestone (quality gate) to ensure that all relevant aspects have been taken into account – for example, also relevant data requirements for which we are not responsible ourselves.
CIP, feedback culture and key figures
247FactoryNet GmbH lives a comprehensive CIP culture; in everything we do, we constantly question whether it could not be done even better. In this sense, the quality management system is also constantly questioned and improved. Potential for improvement is identified from project reviews, employee surveys or other sources. Corresponding measures to optimize the quality management system or its application are consistently taken.