The digital factory creates competitive advantages
A smart factory or intelligent factory aims to achieve a significant increase in efficiency and flexibility. This is primarily achieved by digitally networking the players involved in the value creation process. On the one hand, this digital networking creates transparency, which allows for better reaction and planning, and on the other hand, the possibility to realize optimizations with digital technologies such as AI.
A smart factory or intelligent factory aims to achieve a significant increase in efficiency and flexibility. This is primarily achieved by digitally networking the players involved in the value creation process. On the one hand, this digital networking creates transparency, which allows for better reaction and planning, and on the other hand, the possibility to realize optimizations with digital technologies such as AI.
The digitization of industry is advancing inexorably
The digital factory creates and safeguards jobs, as it enables the international competitiveness of industrial production. For this reason, addressing the possibilities of Industry 4.0 is mandatory for every production manager. The respective potentials and development stages towards a smart factory are very individual and can pursue different objectives. One thing is certain, however: the earlier the start, the greater the competitive advantage.
The Digital Factory makes your production fit for the future – We help you identify and seize your opportunities.
Artificial intelligence (AI) will revolutionize industrial production – Get fit and seize the opportunities!
Better use of production factors ensures greater sustainability of industrial production.
Digital production is by no means devoid of people. On the contrary, humans are one of the actors that will be digitally integrated into the overall process, alongside machines, automated guided vehicles or robots. This means that the digital factory not only requires interfaces to the machines, but it also requires very thoughtful interfaces to the people. Here you can find more about our offer for industrial apps that allow a pragmatic integration of people into the processes of smart production.
The central asset of smart production is digital data. They are the basis for the intelligence of the digital factory, as this enables analysis and automated processing. Read more about OEE optimization and production monitoring here.
In addition, machine failures can be avoided in digital manufacturing by monitoring machine data. Either through a correspondingly distinctive digital maintenance solution or through a predictive maintenance service from the machine manufacturer. More about the 247FactoryNet maintenance software can be found here.
For small and medium-sized manufacturing companies, our digital asset management solution enables:
- Knowhow assurance,
- transparency,
- optimization as well as an
- optimal integration of service partners.
Digitization does not have to be complicated – we stand for pragmatic solutions & put people first.
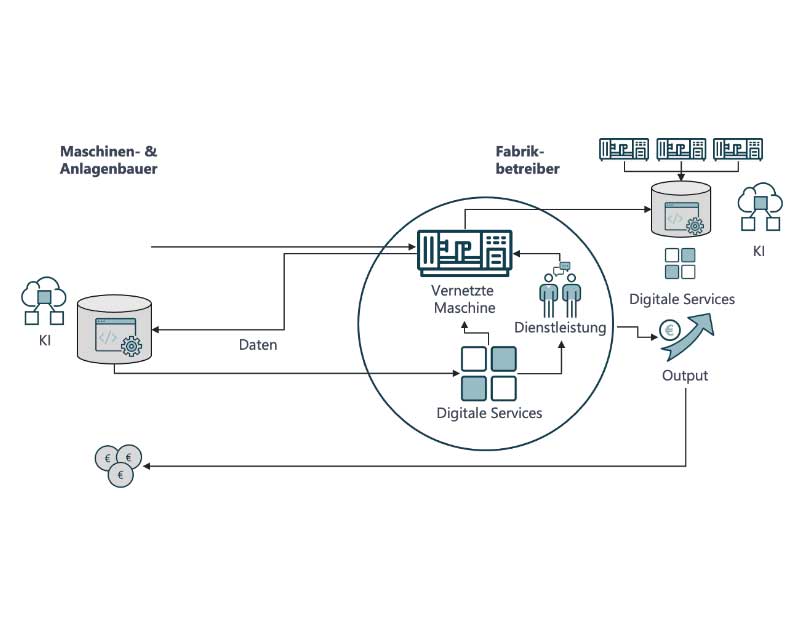
One challenge in the digitalization of a factory is always the digital integration of existing machines. Since there is still no uniform standard regarding the IoT interfaces, a separate connection must often be created for each individual machine. The experts of 247FactoryNet have a lot of experience in the field of control technology, the corresponding interfaces and in the integration of machines or automation cells.
Read more about our offer for machine connectivity for the smart factory here.
Digital factory – for greater efficiency and flexibility
A digital factory is created by digitally mapping the processes, the products and the operating resources required to manufacture the product. The resulting digital data enables much more efficient control of the process and better use of operating resources – right up to predicting a failure of operating resources through predictive monitoring. The digital factory 4.0 enables smart production. This is primarily reflected in three manifestations of the digital factory:
– the integrated product data model
– the digital empowerment of workers
– a data-driven OEE optimization.
For example, digital factory software enables smart manufacturing to be planned in real time – based on the orders to be completed and the machines available at that moment. If a machine breaks down unexpectedly, the digital planning software can immediately create an optimal contingency plan.
An Industry 4.0 digital factory also provides for the integration of suppliers and external processors. For this purpose, the external partners can also be connected to the product data model via appropriate interfaces. Process transparency and planning thus also extend to the external partner companies – they become part of the digital factory. Production, assembly and shipping are digitally recorded and optimized.
Data-driven OEE optimization in particular has enormous potential in the digital factory. This is because, due to digital system integration, potential for OEE optimization measures can not only be determined automatically, but their effect can also be measured immediately. This is a typical field of application in which artificial intelligence will drive Industry 4.0 and the digital factory to a new level of efficiency.
However, all these data-driven services of smart production must also remain comprehensible and manageable for people. So far, no trend can be identified that would mean that even in highly automated, digital factories, people are not still on site at least to monitor and resolve incidents. It is therefore also important to provide people with a meaningful interface for keeping track of the relevant information. This can take the form of a virtual factory in which 3D models display the relevant data in real time, or in the form of dashboards and apps. There are many possibilities; from our point of view, the decisive factor is a package that fits your employees and your requirements.
We will be happy to advise you!